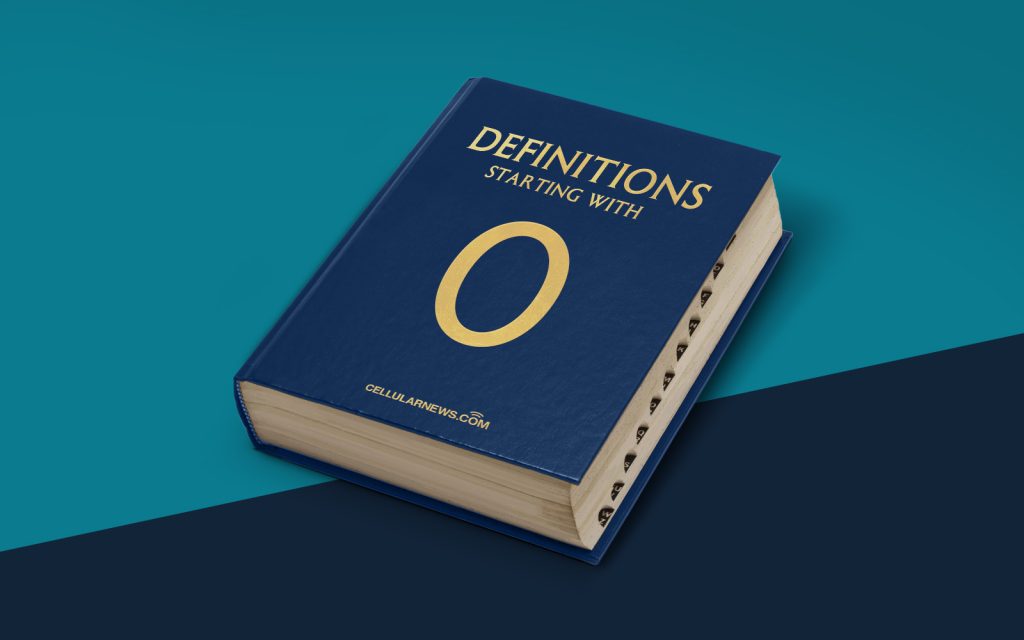
Unlocking the Power of Process Control with OLE for Process Control (OPC)
Process control plays a crucial role in industries such as manufacturing, energy, and pharmaceuticals. It involves monitoring and managing various parameters to ensure efficient and safe operations. To streamline this complex process, many industry professionals turn to OLE for Process Control (OPC). In this article, we will explore the intricacies of OPC and how it can revolutionize process control in various industries.
Key Takeaways:
- OLE for Process Control (OPC) is a widely adopted industry standard for process control systems.
- OPC enables interoperability between software and hardware devices, making it easier to exchange data and integrate different components of a process.
Understanding OLE for Process Control (OPC)
OLE for Process Control (OPC) is an industry standard that facilitates seamless communication between different devices and software used in process control systems. OPC acts as a bridge, enabling interoperability among components such as sensors, programmable logic controllers (PLCs), and supervisory control and data acquisition (SCADA) systems.
OPC utilizes the Object Linking and Embedding (OLE) technology, a Microsoft Windows standard that allows software components to share and exchange data. By leveraging OPC, industrial systems can communicate and exchange real-time data without the need for complex and time-consuming manual configurations.
The Benefits of OPC
Implementing OPC in process control systems offers several significant advantages:
- Improved Efficiency: OPC streamlines the exchange of data between devices, enabling faster and more reliable communication. This real-time data exchange enhances process efficiency and reduces the chances of errors or delays.
- Easy Integration: OPC simplifies the integration of various components within a process control system. It eliminates the need for custom interfaces and protocols, making it easier to connect different devices and software.
- Interoperability: OPC ensures interoperability among different vendors’ devices and software. This enables the use of best-of-breed components without worrying about compatibility issues.
- Scalability: With OPC, adding new components to a process control system becomes less complex. Systems can be expanded or modified without significant disruptions.
OPC in Action
Let’s understand how OPC works in a real-world scenario. Imagine a manufacturing plant that uses various sensors to monitor temperature, pressure, and production rates. The plant also has PLCs controlling machines and a SCADA system collecting and analyzing data.
By implementing OPC, the plant can establish a seamless connection between the sensors, PLCs, and SCADA system. Real-time data from the sensors can be readily transmitted to the SCADA system, where it can be analyzed and used to make informed decisions. The PLCs can receive commands from the SCADA system, ensuring precise control over the machines.
Without OPC, integrating these components would be complex and time-consuming. OPC simplifies the process, making it easier for the plant to achieve optimal efficiency and productivity.
Unlocking the Full Potential of Process Control with OPC
OLE for Process Control (OPC) revolutionizes process control by enabling seamless communication and data exchange between devices and software components. Industries that adopt OPC experience improved efficiency, easy integration, interoperability, and scalability in their process control systems.
Whether you are in manufacturing, energy, or pharmaceuticals, implementing OPC can unleash the full potential of your process control systems. Embrace this industry standard and embrace the power of efficient and streamlined operations.
Do you have any questions about OPC? Feel free to reach out to us!