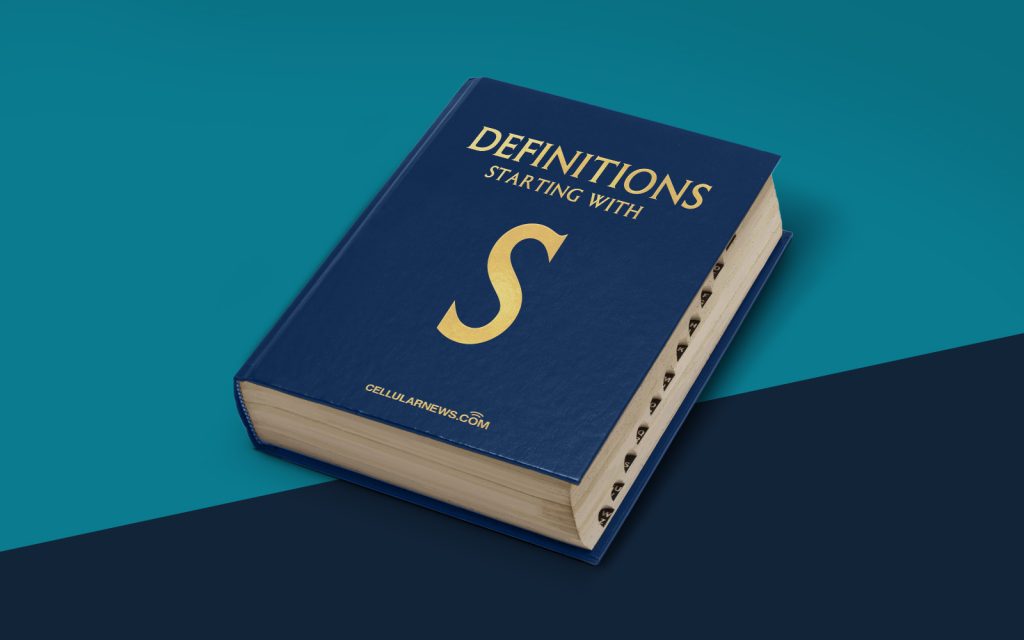
Discovering the Magic of Selective Laser Sintering (SLS)
Have you ever wondered how objects seemingly appear out of thin air, created with intricate designs and impressive precision? Well, wonder no more. Introducing Selective Laser Sintering (SLS), a revolutionary additive manufacturing technique that brings your wildest imaginations to life.
Key Takeaways
- Selective Laser Sintering (SLS) is a 3D printing technique that uses a laser to fuse powdered materials together, layer by layer.
- SLS can create complex and functional objects with a wide range of materials, including plastics, metals, ceramics, and more.
So, what exactly is Selective Laser Sintering (SLS)? In simple terms, it’s a 3D printing method that uses a high-powered laser to fuse powdered materials together, layer by layer, until a solid object is formed. But that barely scratches the surface of what SLS can do. Let’s dive deeper and discover the magic behind this incredible technology.
How Does SLS Work?
At the heart of Selective Laser Sintering is a combination of lasers and thermodynamics. It all starts with a bed of powdered material, typically a polymer or metal. The SLS machine spreads a thin layer of the powder across a build platform, and a high-powered laser beam is directed at specific areas, selectively melting the powder and causing it to solidify.
Once a layer is complete, a fresh layer of powder is spread over the solidified one, and the process continues layer by layer until the final object is formed. This “selective” aspect of the process allows for intricate designs, intricate details, and complex geometries that may be impossible to achieve with traditional manufacturing methods.
Materials That Can Be Used in SLS
SLS offers a wide range of compatible materials, enabling the creation of objects with varying properties and applications. Here are a few examples:
- Plastics: SLS is particularly popular for its ability to produce durable and functional plastic parts. From nylon to polycarbonate, SLS is capable of creating highly resilient objects suitable for a wide range of industries.
- Metals: SLS has expanded its capabilities beyond plastics and can now create metal objects as well, such as stainless steel, aluminum, and titanium. This opens up new possibilities for industries like aerospace and automotive.
- Ceramics: With SLS, intricate ceramic objects can be created, allowing for precise engineering in a field where traditional manufacturing methods struggle to provide the same level of detail.
The versatility of materials available in SLS is one of its greatest strengths. Whether you’re working on a mechanical prototype, a functional part, or a customized product, there’s a material that fits your needs.
The Advantages of Selective Laser Sintering (SLS)
In a manufacturing world that constantly pushes boundaries, SLS stands out as an exceptional technology with a range of benefits:
- Complex Geometries: SLS can create objects with intricate designs and geometries that would be challenging or impossible to achieve with traditional manufacturing methods.
- Prototyping and Customization: SLS is an ideal technique for producing prototypes quickly and efficiently while allowing for customization on demand.
- Functional Parts: With the ability to use a wide range of materials, SLS can create highly functional parts suitable for real-world applications.
- Reduced Waste: The nature of SLS allows for efficient use of materials, reducing waste during the manufacturing process.
It’s no wonder that SLS has become a game-changer in industries such as aerospace, automotive, healthcare, and more. With its ability to produce intricate objects with functional properties, SLS is taking manufacturing to new heights.
In Conclusion
Selective Laser Sintering (SLS) has revolutionized the world of manufacturing, allowing for the creation of complex and functional objects with incredible precision. With its wide range of compatible materials and versatile applications, SLS has become a go-to technology for industries looking to push boundaries and bring innovative designs to life.
So, the next time you marvel at a 3D-printed object, remember that behind the scenes, there’s a Selective Laser Sintering process at work, magically transforming powdered materials into tangible creations.