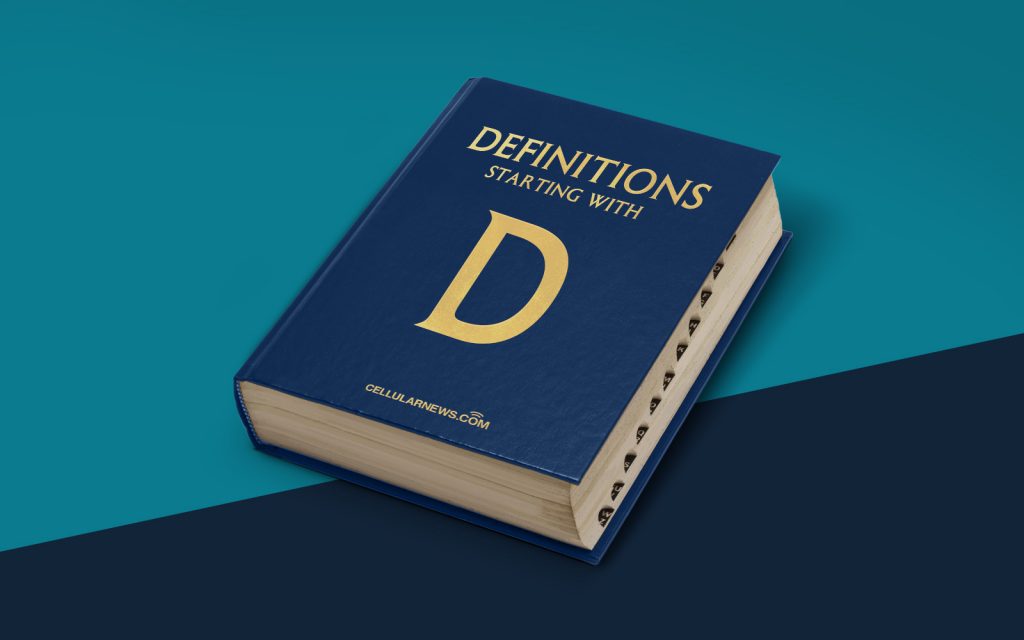
What is Defect Analysis?
Welcome to our “DEFINITIONS” category, where we explore and explain various terms and concepts related to different industries. In this blog post, we will dive into the world of Defect Analysis, a crucial process in identifying and resolving issues. So, what exactly is Defect Analysis?
Defect Analysis is a systematic approach used to identify, study, and rectify defects or faults in a product or process. It is an essential part of quality control and helps businesses deliver high-quality products or services to their customers. Defect Analysis is commonly employed in manufacturing, software development, engineering, and other industries where the quality of output plays a crucial role.
Key Takeaways:
- Defect Analysis involves a systematic approach to identify, study, and rectify defects or faults.
- It is an essential part of quality control in various industries, including manufacturing and software development.
Why is Defect Analysis important?
In any industry, defects can have far-reaching consequences, compromising the quality, safety, and performance of products or services. Defect Analysis helps in understanding the root causes of defects and provides insights into how to prevent them from recurring. By analyzing defects, businesses can:
- Improve Product Quality: Defect Analysis allows businesses to identify and address issues affecting product quality, ensuring that customers receive products that meet their expectations.
- Enhance Customer Satisfaction: By eliminating defects, businesses can improve customer satisfaction and loyalty, leading to repeat purchases and positive word-of-mouth recommendations.
- Reduce Costs: Detecting and rectifying defects early in the production process can save businesses from potential financial losses caused by customer returns, warranty claims, or rework.
- Optimize Processes: Through Defect Analysis, businesses can identify process inefficiencies and make necessary improvements to streamline operations and increase productivity.
How does Defect Analysis work?
Defect Analysis typically follows a systematic methodology to identify, analyze, and resolve defects. The process may vary depending on the industry or sector, but generally includes the following steps:
- Defect Identification: The first step involves identifying defects through inspections, customer feedback, quality control measures, or any other means of defect detection.
- Defect Recording: Once defects are identified, they should be properly recorded, including relevant details such as type of defect, where it occurred, and any associated data.
- Root Cause Analysis: The next step is to determine the root cause or causes of the defect. This may involve analyzing production processes, assembly methods, materials, or any contributing factors.
- Corrective Actions: Based on the root cause analysis, appropriate corrective actions should be implemented. This could include process optimization, training, materials review, or implementing new quality control measures.
- Verification and Validation: After implementing corrective actions, it is important to verify and validate their effectiveness. This may involve retesting, data analysis, or user feedback.
- Continuous Improvement: Defect analysis should be an ongoing process, with organizations continuously learning from defects and making improvements to prevent their recurrence.
By following this systematic approach, businesses can effectively analyze defects, take corrective actions, and continually improve their processes to deliver products or services of the highest quality.
Conclusion
Defect Analysis is a vital component of quality control in numerous industries. By systematically identifying, analyzing, and resolving defects, businesses can enhance their product quality, customer satisfaction, and overall operational efficiency. In an ever-competitive market, a proactive approach to defect analysis can truly set businesses apart by ensuring the delivery of superior products or services that meet or exceed customer expectations.