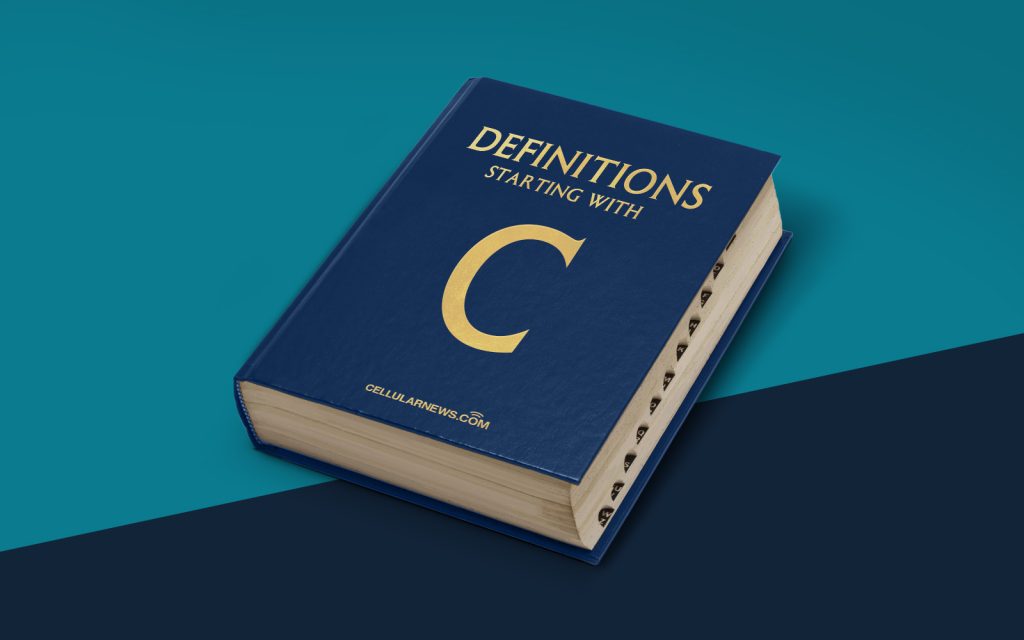
Understanding Computer-Aided Process Planning (CAPP)
In today’s technologically driven world, the integration of innovative software and machinery has revolutionized various industries. One such advancement is Computer-Aided Process Planning (CAPP), which plays a crucial role in streamlining manufacturing processes. But what exactly is CAPP, and how does it enhance efficiency and productivity in the manufacturing sector?
To put it simply, Computer-Aided Process Planning (CAPP) is a specialized software system that assists manufacturers in creating detailed plans and instructions for manufacturing products. It serves as a bridge between Computer-Aided Design (CAD) systems and the actual production process. By automating and optimizing the planning process, CAPP enables manufacturers to reduce errors, minimize costs, and increase productivity.
Key Takeaways:
- CAPP is a software system that facilitates the generation of comprehensive plans and instructions for manufacturing processes.
- Computer-Aided Process Planning bridges the gap between CAD systems and the actual production process.
How Does Computer-Aided Process Planning Work?
Computer-Aided Process Planning utilizes specialized algorithms and databases to generate manufacturing plans based on inputs from CAD systems. Here’s a step-by-step breakdown of how the process typically works:
- Product Design: The process begins with the creation of a product design using CAD software. This design serves as the starting point for subsequent planning stages.
- Feature Extraction: CAPP software intelligently analyzes the CAD model and extracts relevant information regarding features, dimensions, and manufacturing requirements.
- Process Selection: Based on the extracted information, the CAPP system identifies the most suitable manufacturing processes for each component or feature. It takes into account factors such as materials, tolerances, available machinery, and production capabilities.
- Sequence Planning: CAPP determines the optimal sequence in which manufacturing operations should be carried out. It considers factors such as efficiency, cost, and resource availability when determining the sequence.
- Tool Selection: The software selects the appropriate tools and equipment required for each operation, considering factors like tool availability, cost, and efficiency.
- Documentation Generation: Finally, CAPP generates comprehensive instructions, including process sheets, tool lists, machining parameters, and other relevant documentation required for the production team to carry out the planned operations accurately.
The integration of CAPP into manufacturing processes offers several advantages. It reduces planning time, minimizes errors, improves resource utilization, and enhances overall productivity. By automating the process planning stage, manufacturers can focus more on execution and innovation, resulting in improved efficiency and customer satisfaction.
The Future of Computer-Aided Process Planning
As technology continues to evolve, Computer-Aided Process Planning is expected to become even more sophisticated. Advancements in artificial intelligence and machine learning will enable CAPP systems to analyze vast datasets, optimize production plans in real-time, and even predict potential bottlenecks or issues in the manufacturing process. The integration of CAPP with emerging technologies like the Internet of Things (IoT) and digital twins holds immense potential for further enhancing manufacturing efficiency and competitiveness.
In conclusion, Computer-Aided Process Planning (CAPP) is a software system that streamlines the process of creating detailed manufacturing plans and instructions. By automating and optimizing the planning phase, CAPP reduces errors, saves time, and enhances productivity. As technology continues to advance, CAPP systems will play an even more significant role in shaping the future of manufacturing.