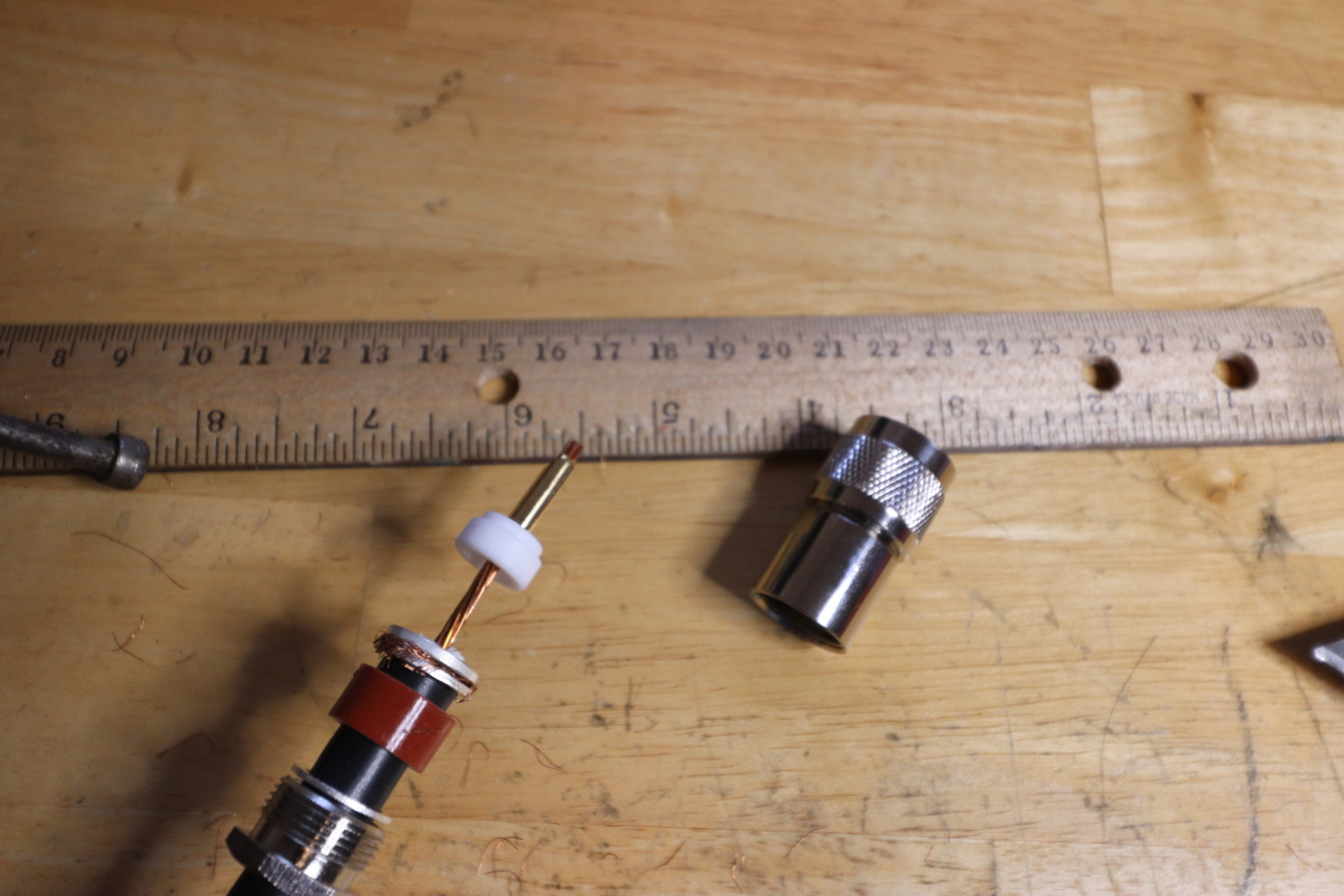
Welcome to our comprehensive guide on how to solder a PL-259 coax connector. Whether you’re a seasoned DIY enthusiast or just starting out, soldering a coax connector is an essential skill to have if you want to properly install or repair your mobile accessories like antennas, cables, or connectors. Soldering ensures a secure and reliable connection, preventing signal loss and interference. In this article, we will walk you through the step-by-step process of soldering a PL-259 coax connector, providing you with valuable tips, techniques, and precautions to achieve professional-grade results. So, let’s dive in and master the art of soldering once and for all!
Inside This Article
- Tools Required
- Materials Needed
- Step 1: Preparing the Coax Cable
- Step 2: Preparing the PL-259 Connector
- Step 3: Inserting the Coax Cable into the Connector
- Step 4: Soldering the Coax Cable to the Connector
- Step 5: Insulating the Coax Cable
- Step 6: Testing the Connection
- Conclusion
- FAQs
Tools Required
When it comes to soldering a PL-259 coax connector, having the right tools is essential. Here are the tools you’ll need to successfully complete the job:
- Soldering iron – A soldering iron is the primary tool used for soldering. It heats up the solder and allows it to flow onto the connections.
- Solder – This is the material used to create a strong connection between the coax cable and the connector. Make sure to use high-quality solder for a reliable and long-lasting connection.
- Wire cutters/strippers – These tools are used to trim and strip the insulation from the coaxial cable, exposing the inner conductor.
- Heat shrink tubing – Heat shrink tubing is used to insulate the soldered connections and provide protection against moisture and damage.
- Heat gun or lighter – These tools are used to shrink the heat shrink tubing and create a tight and secure seal around the connections.
- Flux – Flux is a chemical compound that helps improve the flow of solder and promotes better adhesion between the cable and the connector.
- Wire brush – A wire brush is used to clean the surface of the PL-259 connector, removing any dirt or oxide buildup and ensuring a solid connection.
- Fume extractor or well-ventilated area – Soldering produces fumes that can be harmful if inhaled, so it’s important to work in a well-ventilated area or use a fume extractor to ensure personal safety.
- Safety goggles – Safety goggles should always be worn to protect your eyes from any potential flying debris.
- Safety gloves – Safety gloves provide protection from heat and any potential sharp or hazardous materials.
- Multi-meter – A multi-meter is a useful tool for testing the continuity and quality of the soldered connections.
Having these tools on hand will ensure that you have everything you need to successfully solder a PL-259 coax connector. Remember to always practice proper safety measures while working with soldering equipment.
Materials Needed
Before you start soldering a PL-259 coax connector, it’s essential to gather all the necessary materials. Here’s a list of what you’ll need:
- Soldering iron: A soldering iron is crucial for melting solder and creating a secure connection between the coax cable and the PL-259 connector.
- Solder: Make sure to have high-quality solder to achieve strong and reliable connections. Look for solder with a resin core for easier application.
- PL-259 connector: Purchase a high-quality PL-259 connector specifically designed for coaxial cables. It should have a solid construction and gold-plated contacts for optimum signal transmission.
- Coax cable: Select the appropriate coaxial cable for your specific needs. Ensure that it matches the impedance and frequency requirements of your application.
- Wire cutters/strippers: These tools are necessary for cutting the coax cable to the desired length and stripping the outer sheath to expose the inner conductor.
- Heat shrink tubing: Use heat shrink tubing to insulate the soldered connections and provide additional protection against moisture and physical damage.
- Flux: Flux helps to remove oxidation and impurities from the surfaces being soldered, ensuring a clean and solid connection.
- Heat gun or lighter: You’ll need a heat source to shrink the heat shrink tubing once all the connections are made.
- Small file or sandpaper: A small file or fine-grit sandpaper can be useful for smoothing the edges of the coax cable if necessary.
- Workbench or a stable surface: Find a suitable work area where you can comfortably perform the soldering process.
- Safety equipment: Always prioritize safety when soldering. Wear safety glasses to protect your eyes and work in a well-ventilated area to avoid inhaling solder fumes.
Having all the necessary materials at hand will ensure a smooth and efficient soldering process. Now that you’re fully equipped, let’s move on to the next steps in soldering a PL-259 coax connector!
Step 1: Preparing the Coax Cable
Before you begin soldering the PL-259 coax connector, it’s essential to properly prepare the coax cable. Follow these steps to ensure a clean and secure connection:
1. Start by stripping the outer insulation of the coax cable. Use a cable stripper or a sharp utility knife to carefully remove the outer protective layer, exposing the inner conductor and shield. Make sure to strip back about 1 inch of the insulation.
2. Once the outer insulation is removed, you will see two layers: the inner conductor (usually copper or silver) and the outer shield (usually made of braided wire or aluminum foil).
3. Carefully separate the outer shield from the inner conductor. Gently fold the shield back, exposing the inner conductor.
4. Next, remove any excess dielectric material that may be covering the inner conductor. Use a knife or wire strippers to carefully scrape away the dielectric material, ensuring a clean and exposed inner conductor.
5. After removing the dielectric material, gently twist the strands of the inner conductor, ensuring that they are tightly bundled together. This will provide a solid connection when soldering the coax connector.
6. Finally, use a cable tester or multimeter to check for continuity between the inner conductor and the outer shield. This step ensures that there are no breaks or short circuits in the cable before proceeding with the soldering process.
By properly preparing the coax cable, you are setting the foundation for a strong and reliable soldered connection. Take your time and ensure that each step is performed accurately to guarantee a successful soldering process.
Step 2: Preparing the PL-259 Connector
Before you can start soldering the coax cable to the PL-259 connector, it is important to properly prepare the connector. This involves a few simple steps to ensure a clean and secure connection.
First, make sure you have the necessary tools for this step, which include a small file, a wire cutter/stripper, and a small needle-nose pliers.
The first thing you will want to do is carefully inspect the PL-259 connector to make sure it is clean and free from any dirt or debris. Use the small file to gently remove any oxidation or rough edges that may be present on the connector.
Next, take your wire cutter/stripper and carefully strip off the outer sheath of the coax cable, exposing the inner conductor. Be sure to strip off enough of the sheath to allow for proper insertion into the connector.
Once the inner conductor is exposed, you may notice that it is not perfectly smooth. Use the small file or the wire cutter/stripper to gently remove any burrs or imperfections from the end of the conductor.
Now it’s time to prepare the PL-259 connector itself. Take your small needle-nose pliers and carefully unscrew the connector’s body, exposing the internal components. Set aside the body for now.
Inside the connector, you will see a center pin and a sleeve. Use the pliers to carefully remove the center pin from the connector. Take a moment to inspect the pin for any dirt or debris and clean it if necessary.
With the center pin removed, you can now take the sleeve and slide it onto the coax cable, making sure the cable is properly seated in the sleeve. The sleeve should be positioned towards the end of the cable, just before the exposed inner conductor.
Once the sleeve is in place, slide the PL-259 connector’s body back onto the cable, aligning the threads. Carefully screw the body onto the connector until it is snug. Be cautious not to overtighten as it could damage the connector.
With the PL-259 connector prepared, you are now ready to move on to the next step of inserting the coax cable into the connector and soldering the connection.
Step 3: Inserting the Coax Cable into the Connector
Once you have prepared the coax cable and the PL-259 connector, it’s time to move on to the next step of the process, which is inserting the cable into the connector. This step requires precision and careful handling to ensure a secure and reliable connection.
To begin, take the PL-259 connector and locate the small metal pin in the center. This pin will be used to make a connection with the inner conductor of the coax cable. Insert the pin into the center hole of the connector, making sure it goes all the way in.
Next, you will need to thread the outer braid of the coax cable into the barrel of the connector. The barrel is the cylindrical section that surrounds the pin. Carefully align the braid with the barrel and start threading it in a clockwise direction.
As you thread the braid, make sure it goes all the way into the barrel. It should fit snugly and make full contact with the inner surface. Take your time to ensure that the braid is evenly distributed and not twisted or tangled inside the connector.
Continue threading the braid until it reaches the shoulder of the connector. The shoulder is the wider portion that connects to the body of the connector. Make sure the braid sits securely against the shoulder, providing a solid foundation for the next step of the process.
Once you have successfully inserted the coax cable into the PL-259 connector, give it a gentle tug to check if it is firmly held in place. There should be no movement or slippage. If you feel any looseness, you may need to redo the previous steps to ensure a tight and secure connection.
Take a moment to visually inspect the connection to ensure that the pin is properly aligned with the center hole and the braid is evenly distributed inside the barrel. Any misalignment or unevenness may result in a weak signal or faulty connection.
By carefully following these steps, you can successfully insert the coax cable into the PL-259 connector. This will lay the foundation for the next step of the process, which is soldering the cable to the connector to create a strong and durable connection.
Step 4: Soldering the Coax Cable to the Connector
Now that you have prepared the coax cable and the PL-259 connector, it’s time to solder them together. This step is crucial to ensure a strong and secure connection that will provide optimal signal transmission.
Before you start, make sure you have the necessary tools and materials handy, including a soldering iron, solder wire, and flux. These items will help you achieve a clean and effective solder joint.
To begin, heat up your soldering iron and allow it to reach the desired temperature. This will ensure that the solder melts and flows smoothly, creating a solid bond between the cable and the connector.
Next, apply a small amount of flux to the exposed center conductor of the coax cable. Flux helps in removing any oxidation or contaminants, allowing the solder to adhere properly to the metal surface.
Hold the PL-259 connector with the threaded portion facing upwards. Insert the center conductor of the coax cable into the center pin of the connector. Make sure the conductor is fully inserted and seated securely.
Once the coax cable is in place, use the soldering iron to heat the connector’s base. Apply the solder wire to the joint where the conductor meets the pin and allow it to flow into the connection. Be sure to create a clean and smooth solder bead.
Continue to heat the joint for a few seconds to ensure that the solder properly bonds with the metal. Avoid overheating, as it can damage the cable or the connector. Use a damp cloth or sponge to quickly cool down the joint after soldering.
After soldering, check the connection for any signs of loose solder or bad joints. If necessary, reheat the joint and make any necessary adjustments to ensure a secure and reliable connection.
Once you are satisfied with the soldering, it’s time to move on to the next step of the installation process. Proceed to insulation the coax cable to protect it from any external factors.
Remember, proper soldering is essential for a strong and durable connection. Take your time, follow the instructions, and double-check your work to ensure a successful soldering job.
Step 5: Insulating the Coax Cable
After successfully soldering the coax cable to the PL-259 connector, the next step is to properly insulate the connection. Insulating the coax cable is essential to protect it from damage and ensure optimal signal transmission.
Here are the necessary steps to follow for insulating the coax cable:
- Trim the excess coax cable: Use a cable cutter or sharp knife to trim any excess coax cable extending beyond the connector.
- Slide the heat shrink tubing: Take a piece of heat shrink tubing and slide it over the exposed coax cable and connector. Make sure the tubing covers the exposed area completely.
- Apply heat: Use a heat gun or a heat source such as a lighter to apply heat to the tubing. Move the heat source back and forth along the tubing to evenly distribute the heat.
- Shrink the tubing: As the heat is applied, the tubing will shrink and form a tight seal around the coax cable and connector. Ensure that the tubing has completely shrunk and adhered to the cable and connector.
- Inspect the insulation: Once the tubing has cooled down, inspect the insulation to ensure it is secure and there are no gaps or exposed areas. The insulation should provide a protective covering for the cable and connector.
Insulating the coax cable is crucial to prevent moisture or external elements from corroding the connection and degrading signal quality. It also helps in reducing signal loss and improving the overall performance of the cable.
Remember, a properly insulated coax cable will ensure a secure and long-lasting connection for your audio or video transmissions. Take your time and follow these steps carefully to insulate the coax cable effectively.
Step 6: Testing the Connection
Testing the connection is a crucial step to ensure that the soldered PL-259 coax connector is properly installed and functioning correctly. By conducting a simple test, you can verify the continuity of the connection and identify any potential issues that need to be addressed.
Here are the steps to follow for testing the connection:
- Prepare your testing equipment: You will need a multimeter or a cable tester that is capable of checking for continuity.
- Set your multimeter or cable tester: Configure your testing equipment to measure continuity or resistance.
- Connect the probes to the connector: Place one probe on the center pin of the PL-259 connector and the other probe on the outer shield.
- Check for continuity: Activate the continuity test on your multimeter or cable tester and ensure that it indicates a complete circuit or connection.
- Inspect for any potential issues: Take a close look at the soldering joint, ensuring that there are no cold solder joints, excessive solder, or any visible signs of damage or short circuits.
- Perform a signal test (optional): If applicable, you can also test the signal quality and strength by connecting the cable to the appropriate device and checking for any signal loss or degradation.
By following these steps, you can confirm that the soldered PL-259 coax connector is securely attached and functioning as intended. If you encounter any issues during the testing process, it may be necessary to recheck your soldering work or seek professional assistance to resolve the problem.
Remember, proper testing is essential to maintain a reliable and strong connection for your coaxial cable, whether it is used for telecommunications, audiovisual equipment, or other purposes. Taking the time to test the connection will provide you with peace of mind and ensure optimal performance.
Conclusion
In conclusion, learning how to solder a PL-259 coax connector is an invaluable skill for anyone interested in working with RF cables. By following the step-by-step guide provided, you can confidently tackle this task and ensure a secure and reliable connection. Remember to take your time, practice proper safety precautions, and invest in high-quality tools and materials for the best results.
Once you have mastered the art of soldering PL-259 connectors, you’ll have the ability to customize and repair your own coax cables, saving both time and money. Whether you need to install amateur radio equipment, connect antennas, or set up a satellite system, the knowledge gained from soldering coax connectors will prove indispensable.
So don’t be intimidated by the process, grab your soldering iron and give it a try. With practice, you’ll become a pro in no time, and your coax connections will be strong, reliable, and ready for all your RF communication needs.
FAQs
1. What is a PL-259 coax connector?
2. Why is soldering necessary for a PL-259 coax connector?
3. What tools and materials do I need to solder a PL-259 coax connector?
4. How do I prepare the cable for soldering?
5. Can I use a different type of connector instead of PL-259 for my coax cable?