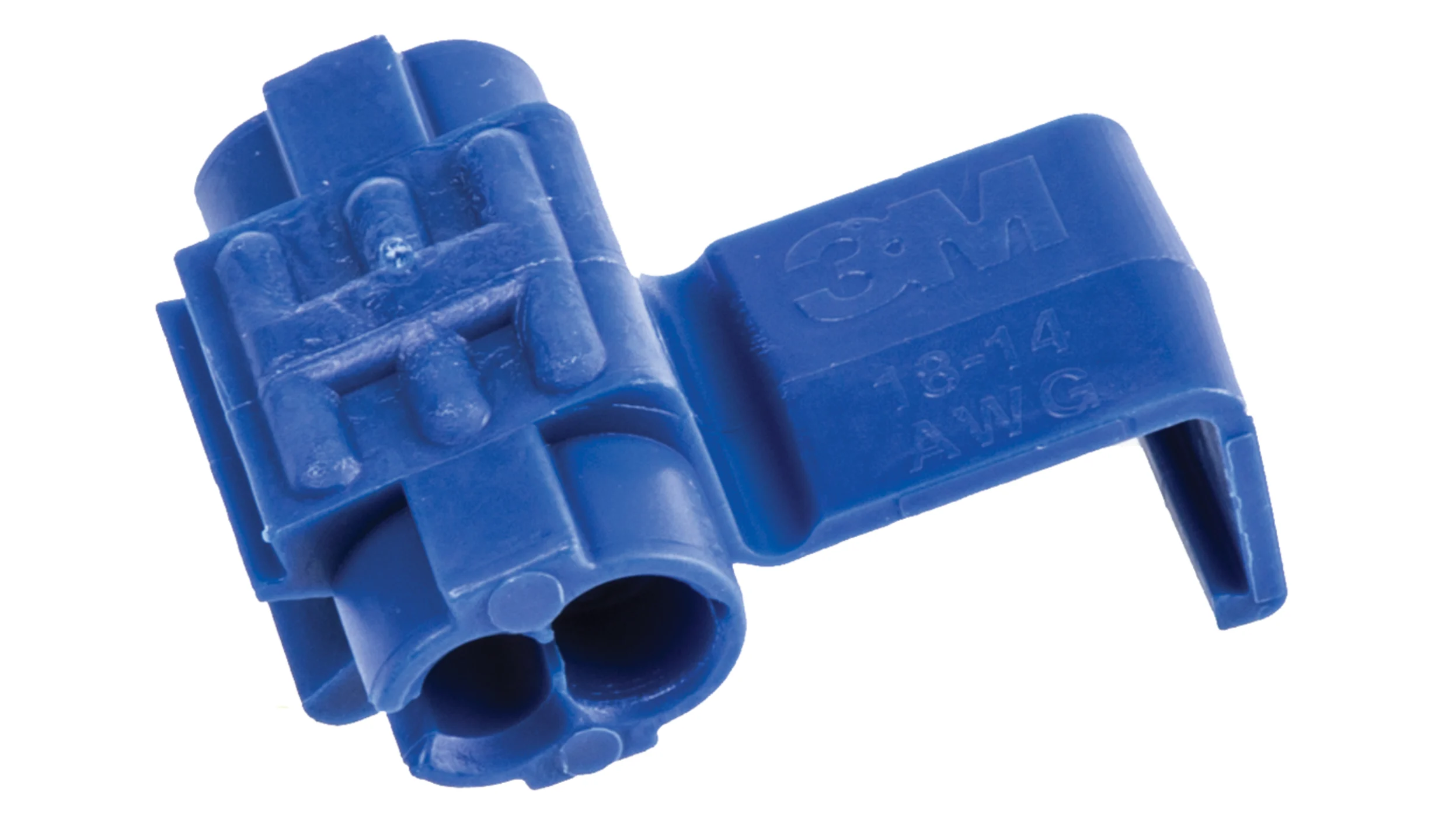
Are you struggling to connect wires securely and efficiently? Look no further than wire splice connectors. These handy accessories have revolutionized the way we connect wires, offering a simple and reliable solution for both professionals and DIY enthusiasts. From electrical systems to automotive applications, wire splice connectors provide a safe and effective way to join wires together.
In this article, we will explore the ins and outs of wire splice connectors, including how to use them effectively. Whether you’re repairing an electrical circuit or adding accessories to your car, understanding how to properly utilize wire splice connectors is essential. So, let’s dive in and discover everything you need to know about these versatile and convenient accessories.
Inside This Article
- What is a Wire Splice Connector?
- Types of Wire Splice Connectors
- Step-by-Step Guide on Using Wire Splice Connectors
- Common Mistakes to Avoid when Using Wire Splice Connectors
- Conclusion
- FAQs
What is a Wire Splice Connector?
A wire splice connector is a device used to connect two or more wires together securely and conductively. It is often used in electrical and electronic applications where joining wires is necessary to create a continuous flow of electricity. Wire splice connectors are available in various types, each designed to accommodate different wire sizes and conductors.
Wire splice connectors are commonly used in automotive, marine, and residential wiring projects. They provide a reliable and convenient solution for connecting wires without the need for soldering or crimping. These connectors are especially useful when joining wires of different gauges or when repairing damaged wires.
Wire splice connectors typically consist of a plastic housing that houses metal or conductive elements. Inside the housing, there are small channels or slots where the wires are inserted. Once inserted, the connector is often secured through a locking mechanism, ensuring a tight and secure connection.
One of the key advantages of using wire splice connectors is their ease of use. Unlike other methods of connecting wires, such as soldering or crimping, no special tools are required. This makes wire splice connectors accessible to individuals of all skill levels, including DIY enthusiasts and beginners.
Furthermore, wire splice connectors provide a durable and reliable connection that can withstand vibrations, temperature changes, and other environmental factors. They are designed to maintain a low resistance connection, ensuring the efficient flow of electricity.
Overall, a wire splice connector is an essential component in various electrical applications. It offers a convenient, reliable, and secure way to connect wires, making it a valuable tool for DIY projects, repairs, and professional wiring installations.
Types of Wire Splice Connectors
Wire splice connectors are essential tools for electrical connections, offering a secure and reliable way to join wires. These connectors come in various types, each designed for specific applications. Here are some common types of wire splice connectors:
- Twist-on wire connectors: Also known as wire nuts, twist-on connectors are perhaps the most well-known type. They consist of a plastic cap with internal threads that twist onto the ends of the wires, creating a secure connection. They are easy to use and can accommodate multiple wires.
- Crimp connectors: Crimp connectors are widely used in automotive and electrical applications. They are made of metal and require crimping tools to compress them onto the wires. They provide a solid and durable connection and are often used in situations where vibration resistance is required.
- Solder seal connectors: Solder seal connectors are heat-shrinkable connectors that combine soldering and insulation in one. They have a heat-activated adhesive that melts and seals the connection when heated. These connectors are ideal for sealing out moisture and providing a waterproof connection.
- Heat shrink connectors: Heat shrink connectors have an inner lining of heat-activated adhesive and a outer heat-shrinkable tubing. When heat is applied, the tubing shrinks and the adhesive melts, creating a tight and insulated connection. These connectors are commonly used in automotive, marine, and outdoor electrical applications.
- Compression connectors: Compression connectors are commonly used in high voltage, high current applications. They require a specialized tool to compress the connector onto the wire, creating a strong and reliable connection. These connectors are preferred in situations where a permanent and robust connection is required.
It’s essential to choose the right type of wire splice connector based on the specific needs of your project. Consider factors like the application, wire size, environmental conditions, and the level of permanence required. Using the appropriate connector will ensure a safe and secure electrical connection.
Step-by-Step Guide on Using Wire Splice Connectors
Wire splice connectors are a valuable tool when it comes to securely connecting and joining wires. Whether you need to repair a damaged wire or create a new electrical connection, wire splice connectors offer a convenient and reliable solution. If you’re new to using wire splice connectors, here is a step-by-step guide to help you get started:
- Gather the necessary tools: Before you begin, make sure you have all the required tools on hand. This typically includes wire splice connectors, wire cutters/strippers, and pliers.
- Prepare the wires: Start by preparing the wires that you want to connect. Use the wire cutters to trim the ends of the wires to the desired length. Then, use the wire strippers to remove a small section of insulation from the ends of each wire.
- Select the appropriate wire splice connector: Depending on the size and type of wires you’re working with, choose the right wire splice connector. There are various options available, such as butt connectors, crimp connectors, and twist-on wire connectors. Refer to the manufacturer’s instructions or consult a professional if you’re unsure which connector to use.
- Insert the wires into the connector: Insert the stripped ends of the wires into the wire splice connector. Make sure that the bare conductors are fully inserted and secured within the connector.
- Secure the connection: Once the wires are inserted, use pliers to firmly crimp or twist the connector, depending on the type of connector you’re using. This will ensure a strong and secure connection.
- Inspect the connection: After securing the connection, carefully inspect it to ensure that no exposed wires or loose connections are visible. This step is crucial to avoid any potential electrical hazards.
- Test the connection: Once the connection is visually inspected, test it to ensure it is functioning correctly. You can use a multimeter or test the electrical circuit to verify that the connection is solid and transmitting the current properly.
- Secure and protect the connection: To provide added protection, you can use electrical tape or heat shrink tubing to secure and insulate the wire splice connector. This will help prevent any exposure to moisture or accidental contact.
- Organize the wires: Finally, organize the wires to ensure they are neatly routed and tucked away. This will help prevent any accidental damage to the wire splice connector or the wires themselves.
By following these step-by-step instructions, you can confidently use wire splice connectors to create secure and reliable connections for your electrical wiring projects.
Common Mistakes to Avoid when Using Wire Splice Connectors
When using wire splice connectors, it’s important to be aware of common mistakes that can compromise the effectiveness and safety of the connection. By avoiding these mistakes, you can ensure a secure and reliable electrical connection. Let’s take a look at some of the most frequent issues to watch out for:
- Not stripping the wires properly: One common mistake is failing to strip the wires to the correct length before inserting them into the splice connector. Make sure to strip the insulation to the recommended length according to the connector’s specifications. This ensures a proper electrical contact and prevents any loose connections.
- Overstuffing the connector: It’s crucial to avoid overstuffing the wire splice connector with too many wires. Each connector has a maximum capacity that should not be exceeded. Overstuffing can lead to a weak connection or even cause the connector to malfunction. Always check the manufacturer’s guidelines for the maximum wire capacity.
- Improper crimping: Another mistake is not crimping the wire splice connector properly. Inadequate crimping can result in a loose connection, which may cause intermittent electrical issues or even pose a safety hazard. Follow the recommended crimping technique and use the appropriate crimping tool to ensure a secure and reliable connection.
- Using the wrong type of wire splice connector: It’s essential to choose the right type of wire splice connector for your specific application. Using the wrong type can lead to compatibility issues and improper connections. Before proceeding, ensure that the connector you are using is suitable for the wire gauge and type.
- Ignoring environmental factors: Wire splice connectors need to be protected against environmental factors such as moisture, heat, and vibrations. Ignoring these factors can lead to corrosion, insulation damage, or even electrical failure. When using wire splice connectors, consider using heat shrink tubing or other protective measures to safeguard the connection from potential hazards.
- Not testing the connection: After making the wire splice connection, it’s crucial to test it to ensure its reliability. Neglecting to test the connection can result in undetected issues that may lead to electrical problems later on. Use a multimeter or a similar testing device to verify the continuity and integrity of the connection.
Avoiding these common mistakes will help you achieve a solid and secure wire splice connection, ensuring optimal safety and performance. Always follow the manufacturer’s instructions and guidelines for the specific wire splice connector you are using and take the necessary precautions to maintain a reliable electrical connection.
Conclusion
Using a wire splice connector is a simple and effective way to join wires together securely. Whether you are tackling a DIY project or working in a professional capacity, these connectors provide a reliable and efficient solution for electrical connections. The step-by-step process outlined in this article demonstrates how easy it is to use wire splice connectors, even for those with limited electrical experience.
By following the correct techniques and guidelines, you can ensure that your wire connections are strong, durable, and able to handle the demands of the electrical current. From household wiring repairs to automotive applications, wire splice connectors offer a convenient and safe way to establish electrical connections without the need for soldering or complicated tools.
Remember to choose the right type of wire splice connector for your specific needs and ensure that the wires are properly stripped and inserted into the connector. With these basic precautions in mind, you can confidently use wire splice connectors to complete your electrical projects with ease and efficiency.
FAQs
1. What is a wire splice connector?
A wire splice connector is a device that is used to join or connect two or more wires together. It provides a secure and reliable connection, ensuring proper electrical conductivity and preventing loose connections or wire breakage.
2. How does a wire splice connector work?
A wire splice connector typically consists of a metal or plastic housing that holds the wires in place. Inside the connector, there are metal contact points or insulation displacement contacts (IDC) that make direct contact with the wire conductors when they are inserted into the connector. This creates a secure electrical connection by piercing through the wire insulation and making contact with the metal conductor.
3. Are there different types of wire splice connectors?
Yes, there are different types of wire splice connectors available, each designed for specific applications. Some common types include:
- Twist-on connectors: These connectors have a threaded design and are twisted onto the wire ends, creating a secure connection.
- Crimp connectors: These connectors require a crimping tool to compress the connector onto the wire, creating a tight and reliable connection.
- Solder connectors: These connectors require soldering to join the wires together. The solder creates a strong and permanent connection.
- Heat shrink connectors: These connectors have a heat shrink tubing that, when heated, shrinks and provides a protective seal around the connection.
4. What are the advantages of using wire splice connectors?
Using wire splice connectors offers several advantages, including:
- Convenience: Wire splice connectors provide a quick and easy way to join wires without the need for soldering or extensive tools.
- Reliability: Splice connectors ensure a secure connection, minimizing the risk of loose or faulty connections that can interfere with electrical performance.
- Versatility: Different types of splice connectors are available to accommodate various wire sizes and applications, making them suitable for a wide range of projects.
- Protection: Some splice connectors, like heat shrink connectors, offer added protection by creating a sealed connection that is resistant to moisture, corrosion, and other environmental factors.
5. What safety precautions should I take when using wire splice connectors?
When using wire splice connectors, it’s important to follow these safety precautions:
- Ensure the power is turned off before working with electrical wires to prevent electrical shocks.
- Select the appropriate splice connector type and size for your wires to ensure a proper fit and secure connection.
- Strip the wires properly and ensure that only the bare conductor is inserted into the connector, with no exposed insulation.
- Follow the manufacturer’s instructions for proper installation and use of the splice connector.
- Regularly inspect the connections to ensure they remain secure and free from damage.
Remember to always prioritize safety when working with electrical components and consult a professional if you are unsure about any aspect of the process.