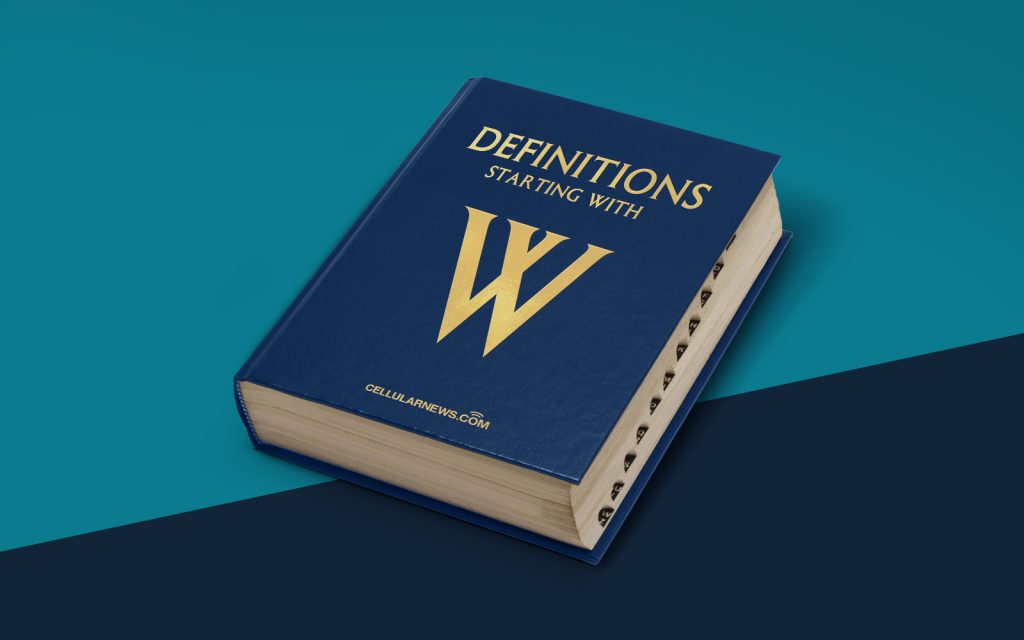
Understanding Wafer: A Recipe for Semiconductor Success
Welcome to the delicious world of wafers! No, we’re not talking about the crispy, thin cookies you might find in the pantry. Instead, we’re diving into the fascinating realm of semiconductor manufacturing. Ever wondered what lies beneath the sleek and shiny exteriors of our smartphones, tablets, and computers? Well, one of the essential ingredients is a humble little slice called a wafer. So, let’s ?break it down? and discover what makes a wafer so special.
Key Takeaways
- A wafer is a thin, circular piece of semiconductor material that serves as the foundation for manufacturing integrated circuits.
- Key ingredients and steps in wafer production include semiconductor material (usually silicon), growth and slicing, fabrication, and testing and packaging.
In a Nutshell?
At its core, a wafer ?is a thin, circular piece of ?semiconductor material?. It serves as a foundation for the manufacturing of integrated circuits (ICs) or microchips. These chips are the building blocks of modern electronics, powering everything from our everyday gadgets to complex machinery and systems. Just like a foundation is vital in constructing a sturdy building, a wafer is a crucial starting point for semiconductor processes.
In semiconductor manufacturing, a wafer undergoes several intricate steps to bring electronic components to life. Semiconductor material, typically silicon, is grown into a cylindrical crystal. This crystal is then sliced, and the resulting disc-shaped pieces are called wafers. These wafers go through various processes of fabrication, including deposition, etching, and doping, to create the desired electrical components.
The Recipe for a Wafer
Now that we know what a wafer is let’s take a look at the key ingredients and steps involved in its creation:
- Semiconductor Material: Silicon is the most commonly used material for wafer production. Its abundance, stability, and excellent electrical properties make it a popular choice in the semiconductor industry. Other materials like germanium and gallium arsenide may also be used for specific applications.
- Growth and Slicing: The first step in wafer production begins with growing a large silicon crystal using specialized techniques like the Czochralski process. Once the crystal is ready, it is sliced into thin, circular wafers. The thickness of a wafer can vary depending on the intended application, but they are typically around 0.75mm thick.
- Fabrication: After the wafers are sliced, they undergo an array of fabrication processes. These processes include cleaning the wafers, depositing thin films of materials on their surfaces, patterning the films using photolithography, implanting impurities to alter the electrical properties, and etching away unwanted materials. These steps are repeated multiple times to build up the layers of the integrated circuit.
- Testing and Packaging: Once the integrated circuit is complete, each individual chip on the wafer undergoes rigorous testing to ensure functionality and quality. Those that pass are then separated from the wafer and packaged into individual housings. These packaged chips are then ready to be used in various electronic devices and systems.
So, next time you hold a cutting-edge smartphone or marvel at the power of a computer, take a moment to appreciate the unassuming wafer that makes it all possible. From its humble beginnings as a slice of semiconductor material, the wafer plays a vital role in the exciting world of electronics and technology.