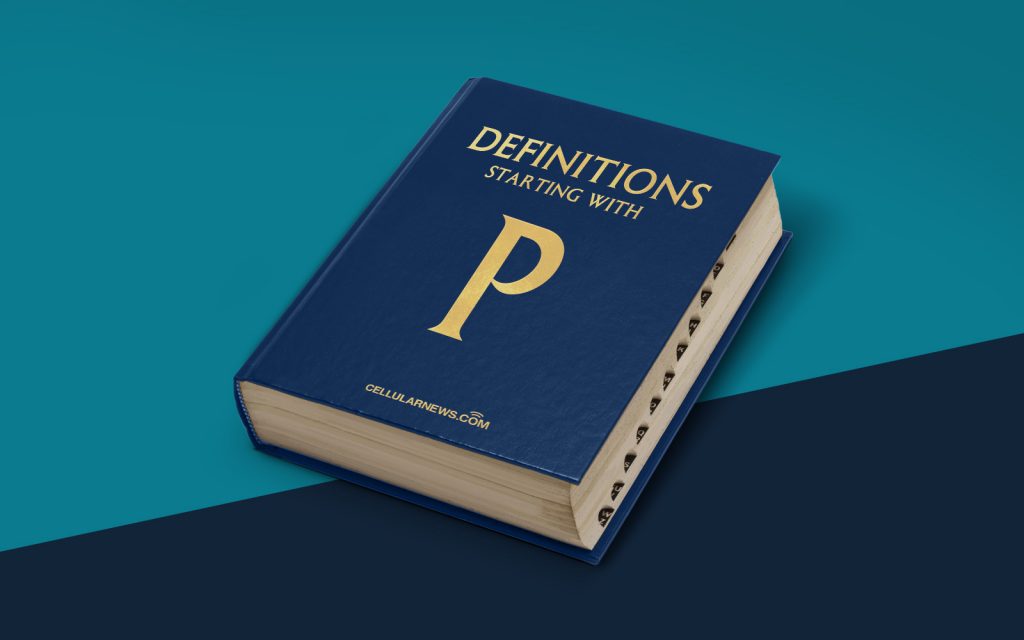
What is Process Specification? A Comprehensive Definition
Welcome to the “Definitions” category on our page! In this blog post, we are going to dive deep into the world of process specification. Let’s unravel the meaning behind this often-used term and explore how it can benefit your business.
Process specification refers to a detailed outline or description of the steps, procedures, and requirements involved in carrying out a specific process or task within an organization. It acts as a blueprint that guides individuals or teams involved in executing the process, ensuring consistency, efficiency, and quality.
Key Takeaways
- A process specification provides a standardized and structured approach for executing tasks within an organization.
- It offers clear instructions, guidelines, and requirements to ensure accuracy, efficiency, and productivity.
The Importance of Process Specification
Now that we understand what process specification means, let’s explore why it is crucial for organizations across various industries:
- Consistency: By documenting each step of a process, a process specification ensures that every individual or team follows the same procedures. This consistency eliminates confusion and results in uniformity in outcomes, fostering quality and reliability.
- Efficiency: A well-defined process specification outlines the most effective and efficient way to complete a task. It eliminates unnecessary steps and streamlines the workflow, saving time and effort. With clear instructions, employees can complete their tasks more quickly, allowing for higher productivity.
- Quality Assurance: Process specifications often include quality control measures, ensuring that tasks are executed accurately and with a high level of precision. This reduces the risk of errors, defects, or rework, resulting in improved quality and customer satisfaction.
- Training and Onboarding: Process specifications serve as valuable training resources for new employees. They provide a comprehensive guide that enables smooth onboarding and reduces the learning curve. New hires can quickly understand the requirements and expectations of their roles, improving efficiency from the start.
- Continuous Improvement: Process specifications are not static documents. They can be reviewed and refined to enhance efficiency and effectiveness continuously. By analyzing the outcomes and identifying areas for improvement, organizations can update their process specifications to optimize performance.
Now that you have a thorough understanding of the importance of process specification, it’s time to evaluate your own organization’s processes. Take a moment to consider whether documenting and optimizing your processes could benefit your team’s productivity, efficiency, and overall success.
Remember, process specification is just one piece of the puzzle when it comes to achieving operational excellence. Stay tuned for more blog posts in our “Definitions” category to expand your knowledge and discover new ways to optimize your business processes.