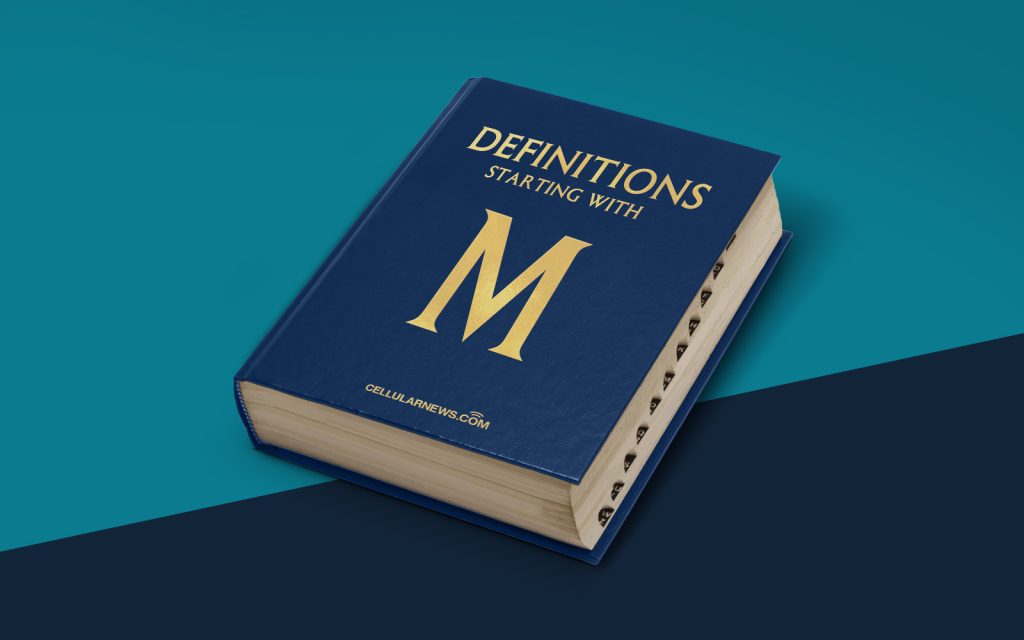
Introduction to Modbus: Unlocking the Power of Industrial Communication
Welcome to the world of Modbus! If you’ve ever wondered what Modbus is and how it works, then you’ve come to the right place. In this article, we will unravel the mysteries of Modbus, providing you with a comprehensive understanding of this widely used communication protocol in the industrial automation field.
Key Takeaways
- Modbus is a widely used communication protocol in industrial automation.
- It facilitates data exchange between devices connected in a network.
What is Modbus?
Modbus is a communication protocol that allows data exchange between devices within a network. Originally developed in 1979 by Modicon, a company now owned by Schneider Electric, Modbus has evolved to become one of the most popular communication protocols used in the industrial automation industry.
Modbus is designed to facilitate communication between devices such as programmable logic controllers (PLCs), remote terminal units (RTUs), and computers. It enables the transfer of data between these devices, allowing them to work together seamlessly and efficiently.
How Does Modbus Work?
Modbus follows a client-server architecture, where the device initiating the communication is called the client, and the device responding to the request is called the server. The communication between these devices is achieved through a master-slave relationship, where the master device sends a request to the slave device and awaits a response.
Here’s a simplified breakdown of how Modbus communication works:
- The master device, typically a PLC or a computer, sends a request to read or write data to a specific slave device.
- The request is sent over a Modbus network, which can be wired (using serial or Ethernet connections) or wireless (using protocols like Modbus TCP or Modbus RTU over Wi-Fi).
- The slave device, which could be a sensor, an actuator, or another PLC, receives the request and processes it.
- If the request is a read operation, the slave device sends back the requested data to the master device.
- If the request is a write operation, the slave device performs the necessary action and acknowledges the master device.
Modbus communication is typically straightforward and lightweight, making it highly efficient for controlling and monitoring devices in industrial settings. Its simplicity and widespread adoption have contributed to its longevity and continued relevance in today’s industrial automation landscape.
Advantages of Modbus
There are several advantages of using Modbus in industrial communication:
- Interoperability: Modbus allows devices from different manufacturers to communicate seamlessly, facilitating system integration and enabling the use of best-in-class components.
- Ease of Use: Modbus’ simplicity makes it user-friendly, with straightforward implementations that are easy to understand and set up.
- Flexibility: Modbus supports various transmission modes and media, including a range of physical and transport layers. This flexibility allows for a wide range of deployment options.
- Cost-Effectiveness: Modbus is a widely adopted open protocol, which means it is often less expensive to implement compared to proprietary alternatives. It also offers excellent support and documentation, reducing maintenance costs.
- Scalability: Modbus can be easily scaled to accommodate a growing number of devices within a network, making it suitable for both small-scale applications and large industrial networks.
In Conclusion
Modbus plays a vital role in the world of industrial communication, enabling seamless connectivity and data exchange between devices in various industrial automation applications. Its widespread adoption, simplicity, and efficiency make it a go-to solution for many engineers and system integrators.
So next time you encounter the term “Modbus,” you’ll have a solid understanding of what it is and how it works. Remember, Modbus is the key that unlocks the power of communication in industrial automation!